What is stereolithography (SLA)?
The term stereolithography refers to an additive manufacturing process that is used to produce high-resolution 3D objects made of plastic. The 3D printing process is based on the property of the polymers used whereby they are cured when exposed to UV light. Stereolithography is particularly suitable for use in prototype construction, since the process allows the mapping of very precise, detailed geometries.
An SLA system consists of a build chamber and a laser scanner unit. The laser hardens the top layer of the liquid plastic based on coordinates that are taken from an existing CAD model. The polymerization process that cures the material is only triggered at points where the synthetic resin used comes into contact with UV light. The build chamber combines several functions: it serves as a storage container for the starting material and is also equipped with a build platform on which the 3D object is created. The platform is mobile in the z direction and is always lowered by exactly one layer of thickness in the course of the building process after the material has been cured by the UV laser. After being lowered, the platform is evenly coated with the material by means of a scraper that moves over the surface.
The component grows into the container layer by layer. Achieving a stable, uniformly cured result at all points requires the coordination of material properties, laser power, beam parameters and scanning speed before production. Incorrect settings can result in layers failing to fuse sufficiently and the product becoming brittle. The laser’s short UV pulses also do not fully cure the plastic. To ensure that the object does not deform during production, fine support structures are also formed from the same material, and are then removed again once the building process is complete. Only final irradiation in a UV cabinet or under a UV lamp gives the component its ultimate properties.
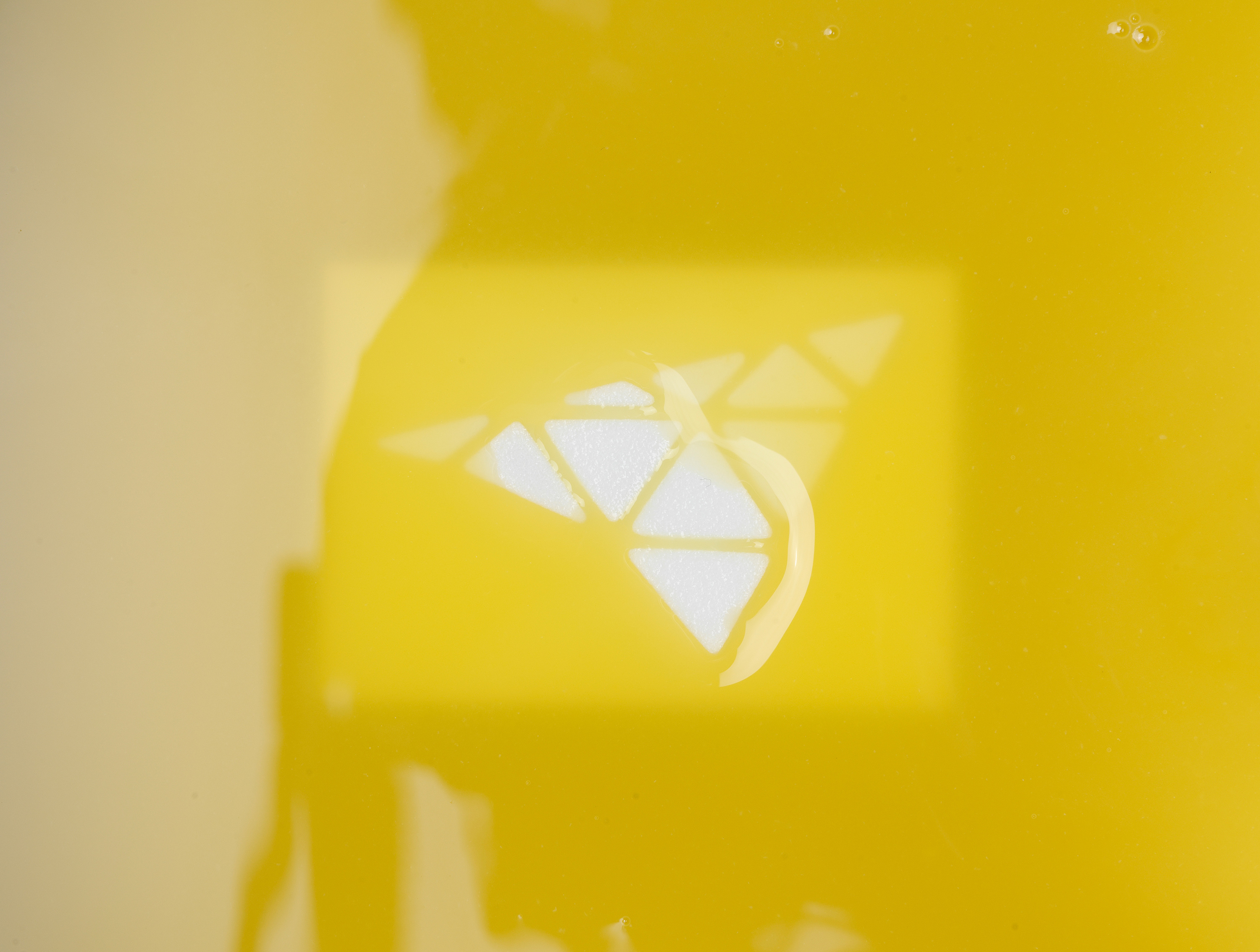