History
Past – The development of stereolithography
Stereolithography (SLA) is the oldest 3D printing process. Japanese engineer Hideo Kodama already published a first version of the technology for the layered construction of a solid plastic object back in 1981. Today, the inventor of 3D printing is however considered to be the American Charles “Chuck” Hull, who patented his method in 1984. The stereolithography process he developed allowed the production of three-dimensional plastic prototypes directly from computer-based data (CAD). The STL file format was developed as a “by-product” in the same process, becoming an additive manufacturing standard that is still in use today. Hull was also one of the founders of the first 3D printing company, 3D Systems, which developed the first commercial 3D printer.
Present – Profitable and fast prototype construction
Stereolithography is still the 3D printing process that allows components to be manufactured with the highest precision. Although SLA is now used for small-scale production (rapid manufacturing) and for the production of individual components, rapid prototyping is still the technology’s core application.
Thanks to its speed and uncomplicated production without the need for finishing, the first prototypes can be profitably manufactured in the early stages of product development.
Future – Obtaining the finished 3D object even faster
Stereolithography is considered as one of the fastest 3D printing methods. Production times that can take several hours to several days for a single component nevertheless have room for improvement. For example, innovative SLA-based printers apparently contribute to avoiding interruptions in the production of 3D objects thanks to a combined supply of oxygen and UV radiation, and instead allow continuous processing of the building material at a consistently high level of precision. SLA printers have so far had to pause between two printed layers to avoid curing additional material. A “dead zone” prevents further unwanted curing of the resin, allowing the irradiation process to continue without interruption. Thanks to the reduction of interruption periods, components are apparently finished up to 100 times faster than with the conventional stereolithography process. Examples of successful developments in this area are Carbon3D (CLIP process) and NewPro3D (ILI™ technology).
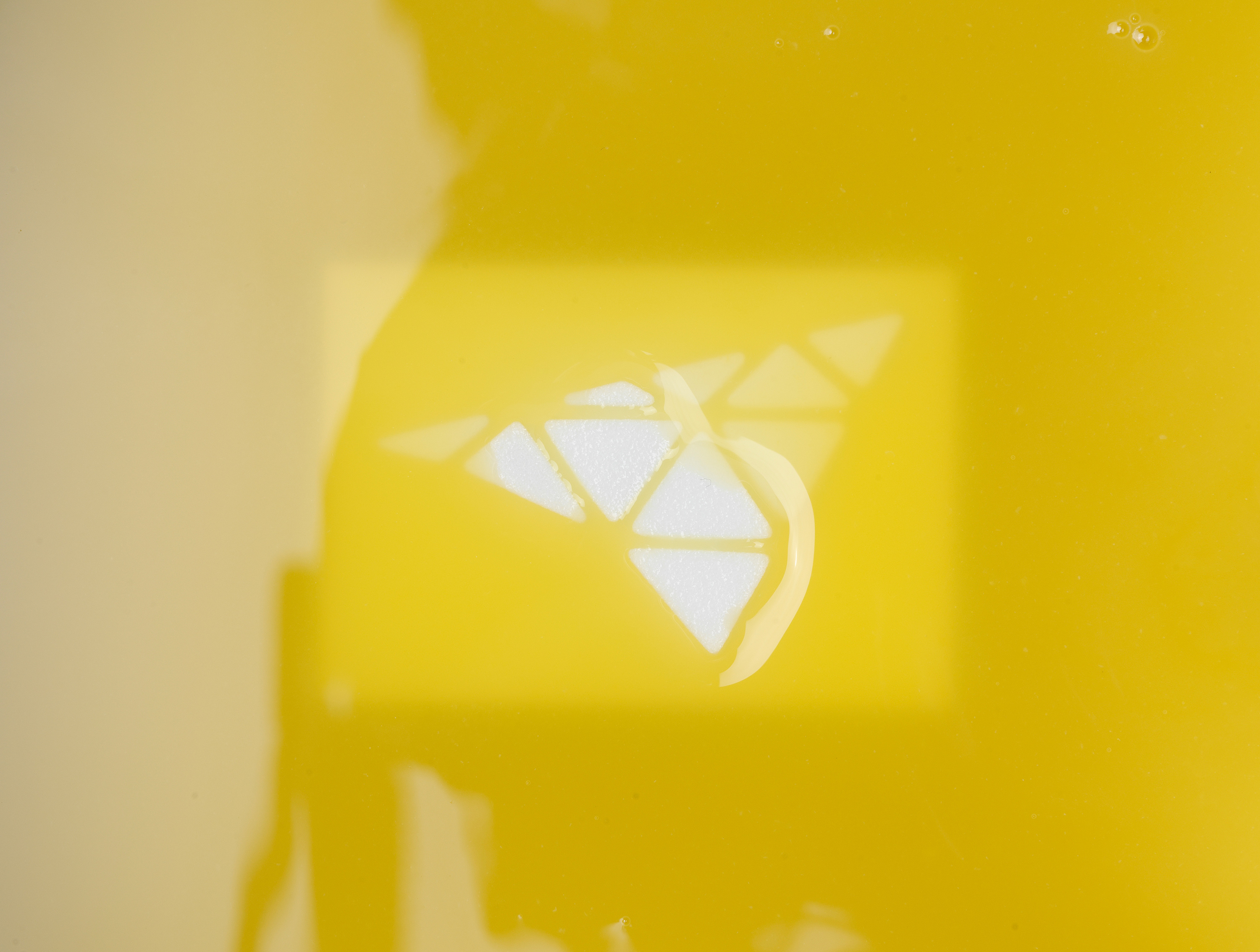