Stereolithography – The First 3D Printing Technique
Delicate Shapes Made of Liquid Plastic
Stereolithography (SLA) is the oldest 3D printing process and is particularly suitable for the representation of especially thin-walled complex geometries. But it is also possible to produce solid components. Liquid photopolymers (e.g. epoxy resin) are used as the material, which are cured layer by layer with the aid of UV light. A 3D model, which must be available as a CAD file, serves as the data basis for the object to be printed. With “slicing”, the model is broken down into individual thin layers that specify the coordinates for the points at which the material is to be cured by UV light. Stereolithography is often used to create detailed demonstration objects or master models, as this technology allows the depiction of particularly delicate structures.
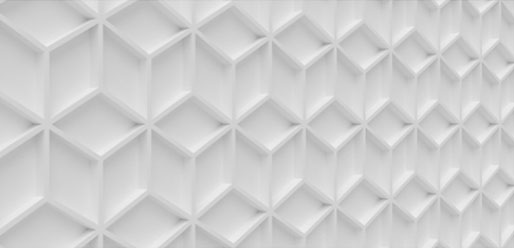
The exceptional advantage of additive manufacturing processes such as stereolithography is the great design freedom. Compared to conventional ablative or recasting processes (e.g. milling, turning, rolling or forging), cavities, undercuts and internal structures can be created easily without causing additional expenditure in production.
Technology with History
The American Charles “Chuck” Hull invented stereolithography in 1983 when, for his job at the time at Ultraviolet Products (UVP), he coated tables with a resilient plastic material that was cured under UV light. He developed his idea of using UV technology to produce objects directly from computer-based data in a small laboratory in his spare time. He wrote a computer program with the aim of targeting the irradiation at the spots where the plastic is to be cured. The basic process developed by Hull has not changed to this day. Liquid plastic is still being cured with coordinated UV radiation. However, the technology behind it has developed rapidly in recent years.