Advantages and disadvantages of the stereolithography process
The stereolithography (SLA) 3D printing process allows the realization of particularly precise and filigree objects, making it ideal for the production of complex prototypes and display models. The use of a liquid starting material results in a particularly smooth surface in the case of SLA-printed 3D objects, generally making subsequent processing superfluous. This saves time and money and also contributes to increased efficiency in terms of material consumption. The object’s precision is limited only by the quality of the system. The finer the laser’s beam diameter, the greater the precision of the printed objects. Theoretically, the layer thickness also limits the objects’ fineness: Liquids cannot be applied to the surface quite as thinly without the coating developing cracks or holes. In practice, however, thicker layer thicknesses tend to be used in order to reduce both building times and costs.
Additive manufacturing allows a considerable degree of design freedom. 3D printing can create hollow spaces or complex internal structures in a single production step and without the use of additional tools. As stereolithography allows the production of particularly clear and transparent objects, the prototypes are ideally suited for the assessment of precisely such internal peculiarities. Furthermore, as several individual parts can easily be combined into larger assemblies, the limited construction space of an SLA system does not affect product development.
All the advantages of stereolithography at a glance:
- Fast implementation of prototypes in early stages of product development
- Single-stage production process produces smooth surfaces even without finishing
- Low material consumption: non-hardened synthetic resin can be reused
- Production of both flexible and rigid 3D objects
- Cost-effective production
- Customized coloring
- Multi-part assemblies are possible
Limitations:
- Depending on the material, components may be brittle
- Support structures can limit design freedom
- Components are only UV-resistant to a limited extent
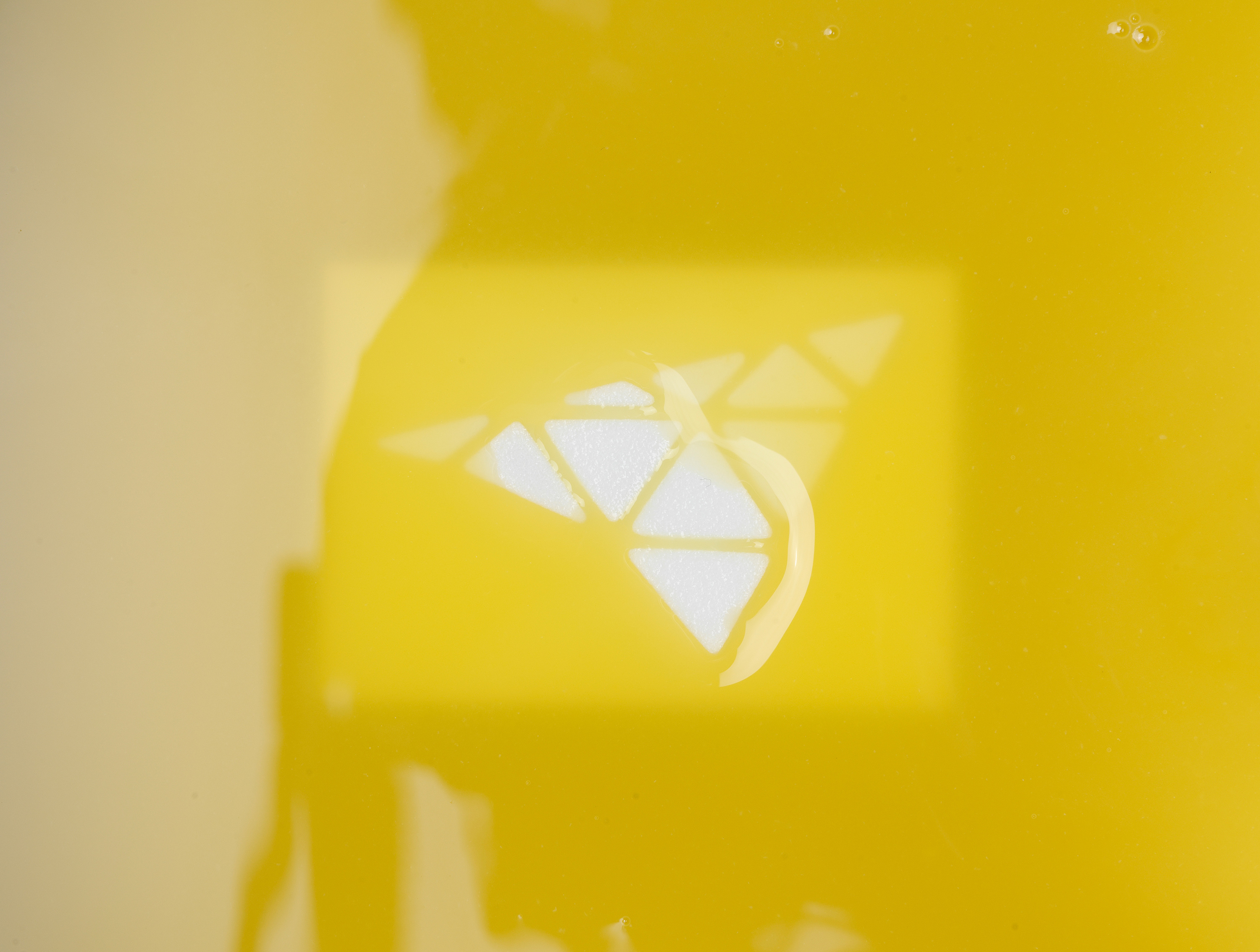